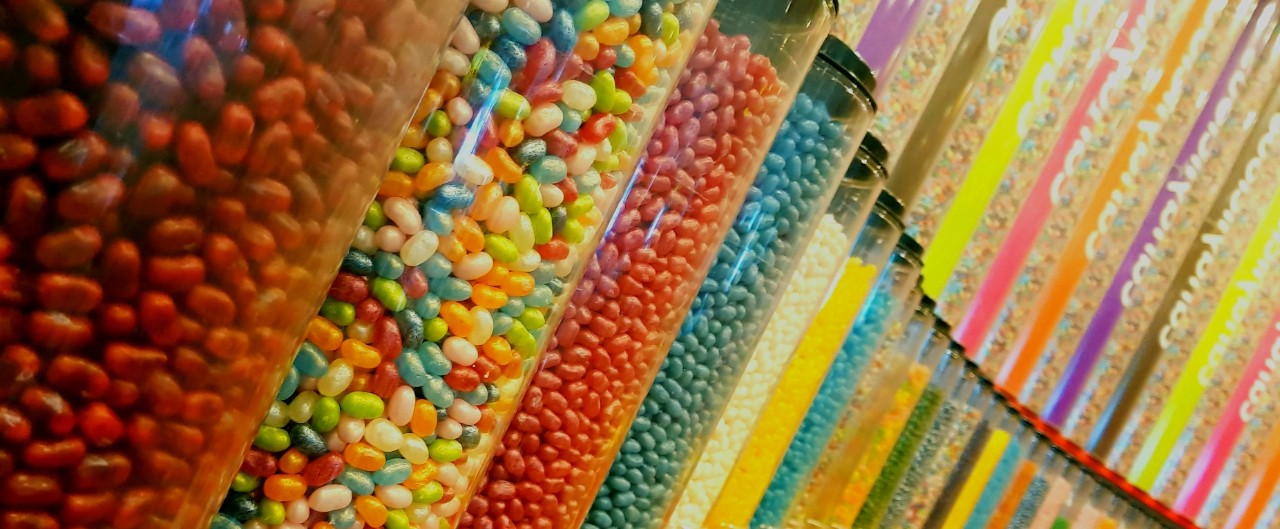
USC Consulting Group(USCCG)은 50년 이상 재무 성과 개선을 통한 실질적인 가치 제공이라는 사명 하에 운영 탁월성을 제고해왔습니다. USCCG는 기업이 공급망 전체의 공정과 운영을 개선하여 잠재력을 최대한 실현할 수 있도록 돕습니다. Minitab의 솔루션은 USCCG가 고객사 문제 해결 및 최적의 운영 수준 실현에서 주도적인 역할을 하는 데 매우 중요하게 기여합니다.
과제
포장 충전업에서 충전 공정 제어는 매우 중요합니다. 과충전은 결과적으로 고객에게 공짜로 제품을 제공하는 것과 같습니다. 다량 작업 공정에서 과충전이 누적되면 연간 수십만 달러에 달하는 손실이 발생할 수 있습니다. 반면 충전 수준이 기준에 미달하면 과태료와 기업 평판 저하로 인해 더 큰 비용이 초래될 수 있습니다.
포장 충전 시 가장 중요한 요건은 소비재의 순수 내용물에 관한 정부 규정을 준수하는 것입니다. 요약하자면, 제품의 충전 중량은 최대 허용 분산(MAV)에 따라 지정된 최소치 이상이어야 합니다. 평균 충전 중량은 라벨 표기 중량 이상이어야 하며, 절대 이에 미달해서는 안 됩니다.
오늘날 많은 기업은 규정상 과태료를 피하고 고객의 충성도를 유지하는 유일한 방법이 과충전이라고 생각합니다. 따라서 기업의 목표는 포장에 표기된 중량에 미달하지 않으면서 이에 최대한 가깝게 제품을 충전하는 것입니다. 이러한 목표는 합리적으로 보이지만, 여러 기업은 이를 달성하는 데 어려움을 겪고 있습니다. 기업이 공정 수용량을 충분히 이해하지 못해서일까요? 아니면 Lean 및 Six Sigma와 같은 적절한 도구와 기법 또는 기술을 활용하여 편차를 줄이고 공정을 관리하지 못해서일까요? 혹은 시행 과정에 문제가 있을까요? 정답은 위 모두입니다.
충전 중량 편차를 최소화 및 제어하고 통계적 모형화를 수행하면 수익금을 상당 부분 늘릴 수 있습니다. Minitab은 충전 중량을 최적화하기 위한 최적의 솔루션으로서 다양한 업계의 고객사가 수백만 달러 상당의 과충전을 줄이는 데 기여했습니다.
Minitab을 활용한 사례
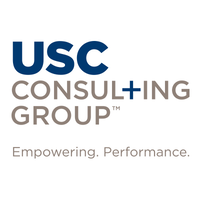
조직
- 공정 개선 전문 경영관리 컨설팅펌
- 플로리다 주 탬파 소재
- 임직원 수 약 200명
과제
포장 충전 시 가장 중요한 요건은 소비재의 순수 내용물에 관한 정부 규정을 준수하는 것입니다. 단위 충전 중량은 지정된 최소 기준 이상이어야 하고, 평균 충전 중량은 라벨 표기 중량 이상이어야 하며 이에 미달해서는 안 됩니다.
사용 제품
Minitab® Statistical Software
결과
- 포장 캔디 제품의 과충전률 50% 이상 감소.
- 연간 재료비 120만 달러 이상 절감.