Headquartered in South Carolina, KYOCERA AVX is a leading global manufacturer of advanced electronic components. KYOCERA AVX has an expansive global footprint comprised of dozens of research, development, and manufacturing facilities spanning more than 15 countries.
Lori Gioia is the Director of Corporate Quality at KYOCERA AVX and has been in this role for almost 5 years. She is a Six Sigma Black Belt with more than 20 years’ experience with quality and continuous improvement. In her role at KYOCERA AVX, Lori leads Quality programs across 30 plus plants globally for KYOCERA AVX.
The Challenge
Kyocera AVX has manufacturing facilities around the world. Each location maintains their own quality management systems and continuous improvement programs. The company’s management had no real time visibility into the different plants to know what was happening with their initiatives. In 2020, KYOCERA AVX came up with the plan to globalize all the systems across the company and began this effort by standardizing its customer complaint system.
The company wanted to:
- Standardize templates and training to provide one voice from the company to customers around the world.
- More easily bring the voice of the customer into R&D and corporate strategic planning.
- Communicate lessons learned more easily between similar locations and businesses.
- Provide management with real time visibility into projects to help with decision-making, removing blocking points and to pinpoint areas for improvement.
The Solution
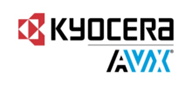
The Organization
- Headquartered in South Carolina
- Has served the automotive, industrial, medical, military, consumer electronics, communications, and transportation markets for nearly 50 years
- Fosters a “zero defect” mindset throughout the organization
The Challenge
Each location maintained their own quality management systems and continuous improvement programs. The company’s management had no real time visibility into the different plants to know what was happening with their initiatives.
Products Used
Minitab Engage®
The Results
- Improved visibility and collaboration across the organization
- New learning opportunities resulting from sharing information and results
- Cost avoidance by reacting faster and more efficiently to customers’ needs